Ferronnerie d’Art
L’expression “ferronnerie d’art” est souvent utilisée de manière générale pour désigner les ouvrages décoratifs en métal forgé, y compris les ouvrages en acier. On pense immédiatement aux portails et aux balustrades élaborés. Cependant, tous les ouvrages en fer forgé ne sont pas décoratifs et l’acier, qui n’a été introduit qu’en 1856, est un matériau très différent, tant par sa forme que par ses performances.
Le fer forgé, qui est la plus ancienne forme de fer utilisée, est le matériau qui a donné son nom à l’âge du fer. Sur le plan architectural, son importance pour les fixations et les attaches a été établie bien avant que le besoin de garde-corps et de balustrades décoratives ne se matérialise, et certains des plus anciens exemples de ferronnerie comprennent des clous et des pointes ainsi que des outils et des pièces agricoles. Cependant, son potentiel décoratif a également été reconnu et certains des premiers exemples de l’utilisation de ce matériau comprennent des bijoux.
De nombreux exemples magnifiques de ferronnerie médiévale subsistent dans les églises, les maisons et d’autres bâtiments, notamment d’énormes charnières en fer forgé, des loquets simplement ornés et de lourdes poignées. Les loquets de fenêtre du XVIIe siècle étaient souvent dotés de plaques arrière en forme de fleur de lys et de motifs de nature en fer forgé sur les poignées. Les fenêtres elles-mêmes et les girouettes en sont d’autres exemples.
En 1689, le travail du fer forgé a connu une révolution, non seulement en termes de ce qui pouvait désormais être réalisé, mais aussi en termes de demande. Jean Tijou, un remarquable ferronnier d’art belge dont le travail était très apprécié par des architectes comme Wren et a été largement imité par une deuxième vague d’artisans tels que William Edney et Thomas Bakewell. Les nouvelles compétences ont notamment permis la production de magnifiques décorations comme des portails et des balustrades. La décoration était très stylisée, avec des motifs symétriques de formes organiques défilantes, généralement constitués de barres sinueuses se terminant souvent par des feuilles et des fleurs. (La ferronnerie est façonnée en trois dimensions par le martelage d’une fine feuille de métal).
FABRICATION ET FORGEAGE
La fonte, le fer forgé, l’acier doux et l’acier inoxydable sont les principales formes de fer utilisées historiquement. Parmi celles-ci, la fonte est la seule qui ne soit pas forgée. Ce matériau présente une structure granulaire résultant du processus de refroidissement, ce qui le rend beaucoup plus résistant. La production commerciale principale de la fonte a commencé à la fin du 18e siècle.
Le fer forgé le plus ancien est connu sous le nom de “fer à charbon“. Il a d’abord été produit par le procédé de “réduction directe”. Le minerai de fer (oxyde de fer avec diverses impuretés) était fondu en le chauffant avec du charbon de bois dans de petits fours. Le charbon de bois (essentiellement du carbone) réduisait l’oxyde de fer en fer, dégageant du monoxyde de carbone au cours du processus. Une grande partie des impuretés minérales qui comprenaient notamment du silicate de fer. Après la fusion le fer étaient forgés en les chauffant jusqu’au rouge, puis en les battant pour en faire de longues barres. Chaque barre était ensuite coupée en longueurs plus courtes, regroupées et reforgées. Le processus pouvait être répété de nombreuses fois. À chaque forgeage, une partie était éliminée et les fins résidus restants s’incorporaient au fer, formant ensemble la microstructure fibreuse caractéristique qui confère au fer forgé sa résistance à la traction. Le fer produit pouvait être d’excellente qualité, mais c’était un processus laborieux.

Les hauts fourneaux introduits de Belgique vers 1400 ont permis d’augmenter la production et de réduire considérablement les impuretés. Le minerai de fer était d’abord fondu avec du charbon de bois dans le haut fourneau, comme auparavant, pour produire de la fonte “brute”. Mais dans un deuxième temps, le fer était affiné par “décarburation”, c’est-à-dire l’élimination du carbone, avant d’être forgé.
D’autres améliorations ont été apportées à la production, notamment l’introduction de lourds marteaux posés sur un point d’appui pour battre le métal semi-fondu et éliminer les impuretés. Les laminoirs à eau, introduits à la fin du XVIe siècle, ont contribué à mécaniser le processus de forgeage ; les barres chauffées au rouge passaient entre deux lourds rouleaux (le “laminoir”), devenant chaque fois plus longues et plus fines. Une forme modifiée de charbon, a été utilisé à la place du charbon de bois par Abraham Derby à Coalbrookdale après 1709, car les réserves de bois pour le charbon de bois neuf s’épuisaient rapidement.
Au milieu du 19e siècle, le fer forgé était considéré comme relativement cher. Le fer coulé, bien que faible en tension, était produit en masse et était donc beaucoup moins cher. Comme il s’agit d’une fonte, les formes qui pouvaient être produites étaient très différentes, mais elles n’en étaient pas moins belles, et pour la plupart des usages décoratifs, la fonte offrait une solution plus rentable. Pour les applications structurelles, la fonte a remplacé le fer forgé lorsque les charges étaient supportées en compression, comme les colonnes, mais le fer forgé a continué à être utilisé en tension, par exemple dans le toit d’une véranda. Puis, en 1856, Henry Bessemer a inventé le convertisseur Bessemer, qui a permis de produire de l’acier à un coût plus bas que jamais. Contrairement au fer forgé, l’acier
ne contient pas de scories et sa teneur en carbone est plus élevée que celle du fer puddlé (ancien procédé d’affinage de la fonte). Par conséquent, il est plus dur et plus résistant à la traction. À la fin du XIXe siècle, le fer forgé était en déclin.
CONSERVATION ET RÉPARATION
Parce que le métal est si dur, il engendre un faux sentiment de sécurité. Le métal est souvent fragile, en particulier lorsqu’il est affaibli par la rouille. Les dommages peuvent être cachés par la rouille et la peinture, et les joints sont plus vulnérables lorsque l’eau a été aspirée par capillarité, ce qui rend le matériau susceptible de subir d’autres dommages lorsqu’il est démonté pour être réparé. En outre, les méthodes de nettoyage et de réparation ont tendance à être conçues pour augmenter la dureté du matériau, mais peuvent être extrêmement dommageable.
Il peut être possible d’effectuer des réparations mineures sur place, mais pour la plupart des travaux importants, les ferronneries doivent être démontées et nettoyées afin qu’une évaluation complète de leur structure puisse être effectuée en atelier. Lorsque la ferronnerie est ancrée dans une maçonnerie humide, il est essentiel de l’enlever, de la réparer et de la refixer, car le fer rouillé se dilate plusieurs fois par rapport à sa taille initiale, exerçant ainsi une pression énorme sur la maçonnerie environnante. Heureusement, lorsque les fixations étaient enfoncées dans la pierre, le trou était généralement rempli de plomb fondu, et il est possible de l’enlever en chauffant le métal jusqu’à ce que le plomb fonde.
Avant d’enlever le fer forgé (et en fait avant tout travail sur cet élément ou tout autre élément historique), son état, sa conception et sa relation avec le reste de la structure doivent être soigneusement étudiés et documentés – au moins par des photographies. Ce document sera essentiel pour la remise en place ultérieure de l’élément et pourra s’avérer inestimable si d’autres dommages devaient survenir.
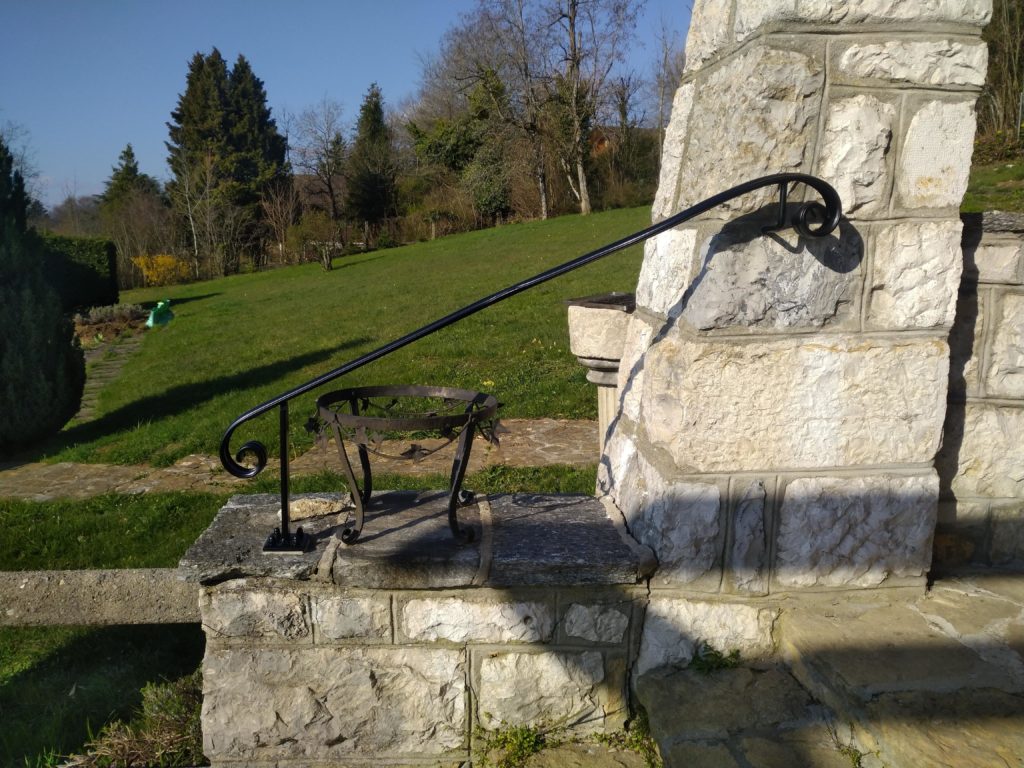
Les joints métal sur métal étaient réalisés soit en soudant une pièce de métal à une autre dans la forge, soit en utilisant une fixation mécanique. Il s’agissait de joints à tenon et mortaise (les premiers travaux étaient fortement influencés par les techniques de menuiserie), de rivets et de colliers. Un rivet est essentiellement un axe à tête plate qui serre deux pièces de métal ensemble par le milieu, et les colliers obtiennent un résultat similaire en s’enroulant étroitement autour de deux ou plusieurs pièces parallèles. Les assemblages qui reposent sur une fixation mécanique peuvent sembler constituer un moyen simple et réversible de démonter une pièce pour la réparer. Cependant, une fois cassé, il peut être extrêmement difficile de redonner sa forme d’origine à un objet complexe tel qu’un portail, c’est pourquoi on évite autant que possible de le démonter davantage.
NETTOYAGE
Le sablage, la méthode la plus couramment utilisée pour enlever la peinture, peut être très dommageable car elle risque d’enlever non seulement la peinture mais aussi la ” calamine ” d’origine, la surface extérieure du fer formée dans la forge. Même les œuvres vieilles de 300 ans conservent généralement 90 % de leur écaille de laminage, et comme il s’agit d’une surface protectrice à part entière, son élimination peut entraîner une dégradation accélérée. Sa surface peut également contenir des caractéristiques d’un intérêt considérable, comme les marques de limage d’origine, et sur les matériaux conçus pour un usage interne, elle conservera son poli d’origine.
Utiliser des agents chimiques choisis en fonction du type de peinture et de la nécessité d’éviter d’endommager le métal lui-même. Une fois la peinture enlevée, il faut veiller à ce que les résidus chimiques soient également éliminés ou neutralisés.
La rouille s’enlève le plus facilement après l’application de chaleur, car la calamine ne se dilate pas autant que le fer, ce qui fait que son adhérence est suffisamment relâchée pour qu’on puisse l’enlever à la brosse.
RÉPARATIONS ET COMPOSANTS MANQUANTS
Effectuer toutes les réparations en utilisant le même matériel et les mêmes techniques qu’à l’origine. Cependant, les réparations du fer puddlé et du fer au charbon de bois peuvent être effectuées avec succès avec le fer puddlé, car les deux matériaux sont de nature relativement similaire. La fonte au charbon est difficile à obtenir, alors qu’il existe un approvisionnement relativement abondant de fonte victorienne puddlée provenant, par exemple, de l’ingénierie victorienne démantelée ces dernières années.
L’acier doux et l’acier inoxydable peuvent être soudés au fer forgé, et l’utilisation de pointes en acier inoxydable peut être appropriée lorsque des fixations scellées dans une maçonnerie humide ont rouillé. Cependant, il s’agit là d’une exception et, en général, l’acier ne convient pas à la réparation du fer forgé car les propriétés des deux matériaux sont très différentes, ce qui affecte à la fois l’apparence de l’ouvrage fini et ses performances. En particulier :
- L’acier doux est plus enclin à la rouille que le fer forgé.
- Les barres d’acier (doux ou inoxydable) ont tendance à être utilisées dans des tailles de section standard, ce qui donne un aspect uniforme qui n’a pas le caractère des anciennes barres forgées à la main, et ne correspondent pas aux tailles de section impériales du fer forgé laminé.
- Le fer forgé est généralement assemblé à l’aide de joints soudés à la forge, les sections étant fixées ensemble sur place.
- L’acier ne se soude pas dans le feu aussi facilement que le fer forgé, de sorte que le soudage à l’arc tend à être utilisé partout.
- Il en résulte une approche différente de la conception ainsi que des différences dans les détails qui sont facilement reconnaissables dans la plupart des travaux modernes réalisés par des artisans non spécialisés.
Il n’est pas pratique de souder les ouvrages en fer forgé dans la forge. Le fer forgé peut être soudé à l’arc sur place, si nécessaire. En raison de la nature fibreuse du fer forgé, il est très important que toute soudure s’étende sur toute la surface et profondeur du matériau, afin de garantir que tous les éléments laminés de l’original sont reliés. Les soudures superficielles n’ont aucune résistance, car la soudure repose sur l’épaisseur d’une seule lamelle, qui est souvent moins épaisse qu’un fil de coton.
Lorsque le soudage à l’arc est nécessaire, il ne faut pas utiliser de fils ou de tiges en acier doux, car l’acier se rouille. Il faut utiliser soit des métaux dissemblables, soit un fil ou une tige en alliage de fer non corrosif.
PROTECTION
Une protection complète contre les intempéries est essentielle pour toutes les ferronneries extérieures. Lors du réassemblage, les faces intérieures des éléments assemblés peuvent être recouvertes d’un mastic silicone moderne au lieu du mastic de plomb rouge utilisé traditionnellement. Toutes les surfaces doivent être soigneusement peintes, en prenant soin d’inclure le dessous de couche. Une grande variété de peintures est disponible pour réduire le risque de rouille, notamment des peintures à base de résine et des sous-couches riches en plomb rouge ou en zinc. Il faut également veiller à éviter les points de collecte de l’humidité et, une fois peints, les renfoncements peuvent être remplis d’un produit de remplissage approprié tel que la poix (la solution traditionnelle) ou une résine époxy.
La galvanisation est généralement considérée comme inappropriée pour les accessoires historiques, en particulier pour les pièces délicates et très détaillées, principalement parce que le travail du métal doit être plongé dans l’acide avant d’être galvanisé. L’acide attaque la surface, endommageant les éléments plus vulnérables, notamment ceux retenus dans des poches par des formes plus complexes.
Les aménagements intérieurs étaient parfois protégés par des huiles ou des cires. Selon John et Nicola Ashurst, dans le manuel technique du patrimoine anglais, “un traitement traditionnel pour le fer forgé consistait à gratter, ébrécher ou décaper la surface jusqu’à ce que le tartre et les substances étrangères soient éliminés. Une couche épaisse d’huile de lin était appliquée, puis le fer était chauffé et essuyé avec de la toile d’émeri. Enfin, une combinaison de cire d’abeille et d’huile de lin bouillie était frotté sur la surface”.